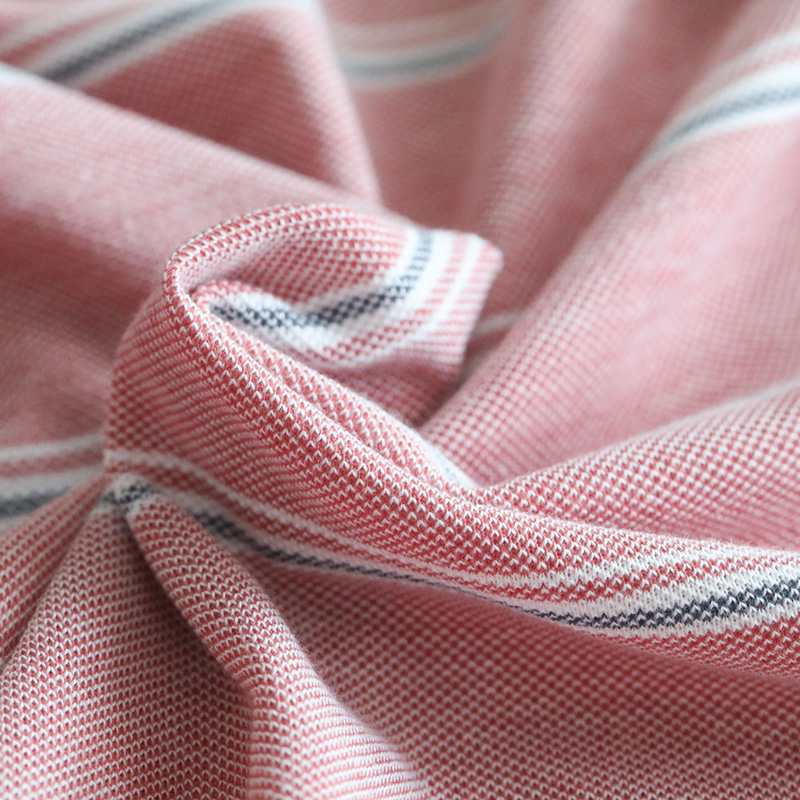
YARN DYE
Yarn dye refers to the process of first dyeing the yarn or filament, and then using the colored yarn to weave the fabric. It is different from the printing and dyeing method where the fabric is dyed after weaving. Yarn-dyed fabric involves dyeing the yarn before weaving, resulting in a more unique style. The colors of yarn-dyed fabric are often vibrant and bright, with patterns created through color contrasts.
Due to the use of yarn dye, yarn-dyed fabric has good colorfastness as the dye has strong penetration.
Stripes and colorful linen gray in polo shirts are often achieved through yarn-dye techniques. Similarly, cationic yarn in polyester fabrics is also a form of yarn dye.
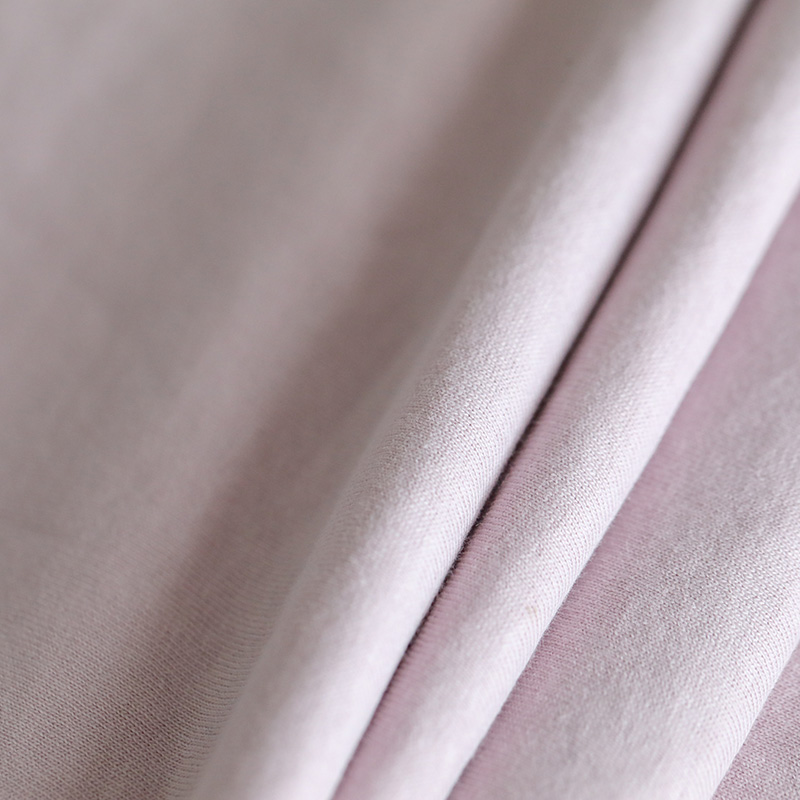
Enzyme Wash
Enzyme wash is a type of cellulase enzyme that, under certain pH and temperature conditions, degrades the fiber structure of fabric. It can gently fade color, remove pilling (creating a "peach skin" effect), and achieve a lasting softness. It also enhances the drape and luster of the fabric, ensuring a delicate and non-fading finish.
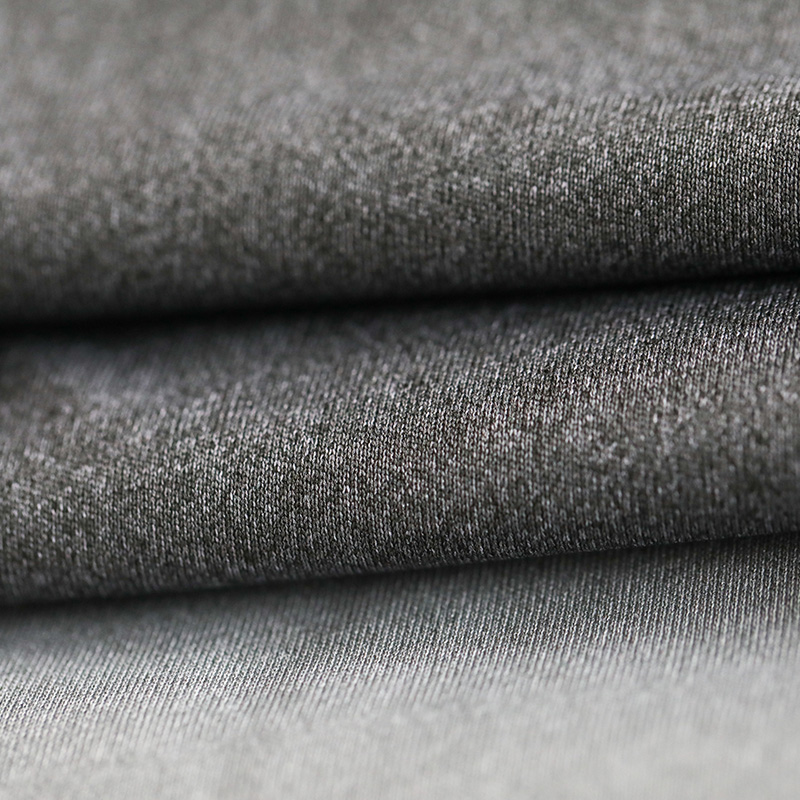
Anti-pilling
Synthetic fibers have high strength and high resistance to bending, which makes the fibers less likely to fall off and form pills on the surface of textile products. However, synthetic fibers have poor moisture absorption and tend to generate static electricity during dryness and continuous friction. This static electricity causes the short fibers on the surface of the fabric to stand up, creating conditions for pilling. For example, polyester easily attracts foreign particles and pills form easily due to static electricity.
Therefore, we use enzymatic polishing to remove the microfibers protruding from the surface of the yarn. This greatly reduces the surface fuzz of the fabric, making the fabric smooth and preventing pilling. (Enzymatic hydrolysis and mechanical impact work together to remove the fluff and fiber tips on the fabric surface, making the fabric structure clearer and the color brighter).
In addition, adding resin to the fabric weakens the fiber slippage. At the same time, the resin evenly cross-links and aggregates on the surface of the yarn, making the fiber ends adhere to the yarn and reducing pilling during friction. Therefore, it effectively improves the fabric's resistance to pilling.
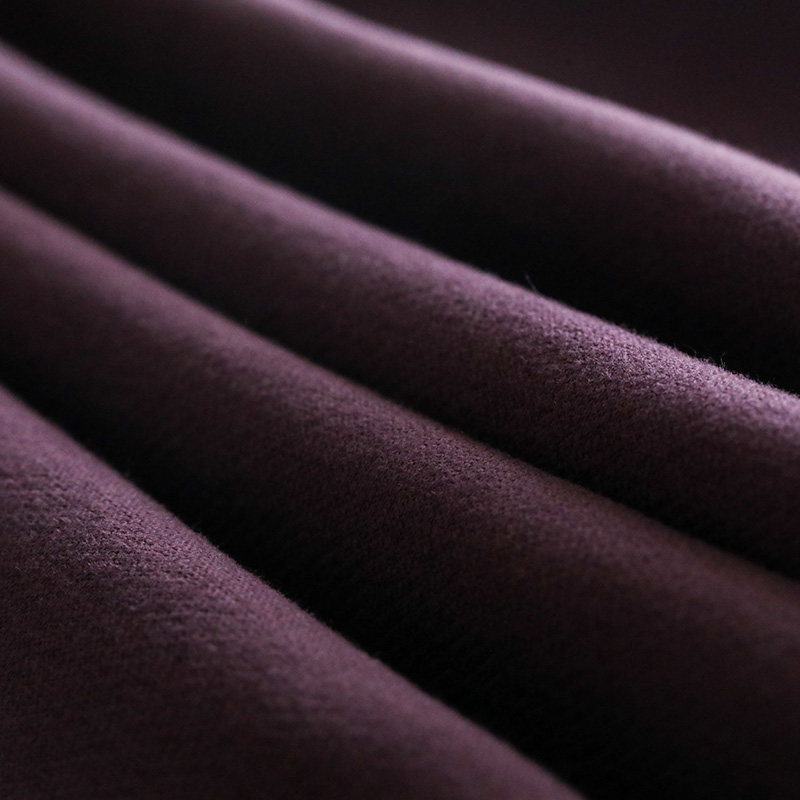
Brushing
Brushing is a fabric finishing process. It involves frictional rubbing of the fabric with sandpaper wrapped around a brushing machine drum, which changes the surface structure of the fabric and creates a fuzzy texture resembling the skin of a peach. Therefore, brushing is also known as PeachSkin finishing and the brushed fabric is referred to as PeachSkin fabric or brushed fabric.
Based on the desired intensity, brushing can be categorized as deep brushing, medium brushing, or light brushing. The brushing process can be applied to any type of fabric material, such as cotton, polyester-cotton blends, wool, silk, and polyester fibers, and to various fabric weaves including plain, twill, satin, and jacquard weaves. Brushing can also be combined with different dyeing and printing techniques, resulting in dispersed printing brushed fabric, coated printing brushed fabric, jacquard brushed fabric, and solid-dyed brushed fabric.
Brushing enhances the fabric's softness, warmth, and overall aesthetic appeal, making it superior to non-brushed fabrics in terms of tactile comfort and appearance, particularly suitable for use in winter.
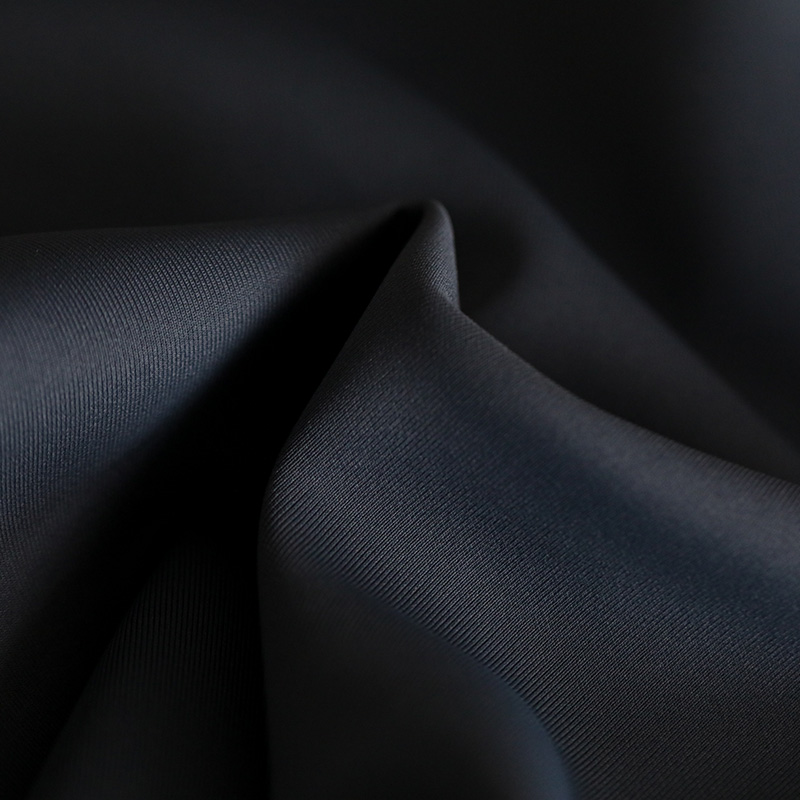
Dulling
For synthetic fabrics, they often have a shiny and unnatural reflection due to the inherent smoothness of synthetic fibers. This can give people the impression of cheapness or discomfort. To address this issue, there is a process called dulling, which is specifically aimed at reducing the intense glare of synthetic fabrics.
Dulling can be achieved through fiber dulling or fabric dulling. Fiber dulling is more common and practical. In this process, titanium dioxide dulling agent is added during the production of synthetic fibers, which helps to soften and naturalize the sheen of polyester fibers.
Fabric dulling, on the other hand, involves reducing the alkaline treatment in dyeing and printing factories for polyester fabrics. This treatment creates uneven surface texture on the smooth fibers, thereby reducing the intense glare.
By dulling synthetic fabrics, the excessive shine is reduced, resulting in a softer and more natural appearance. This helps to improve the overall quality and comfort of the fabric.
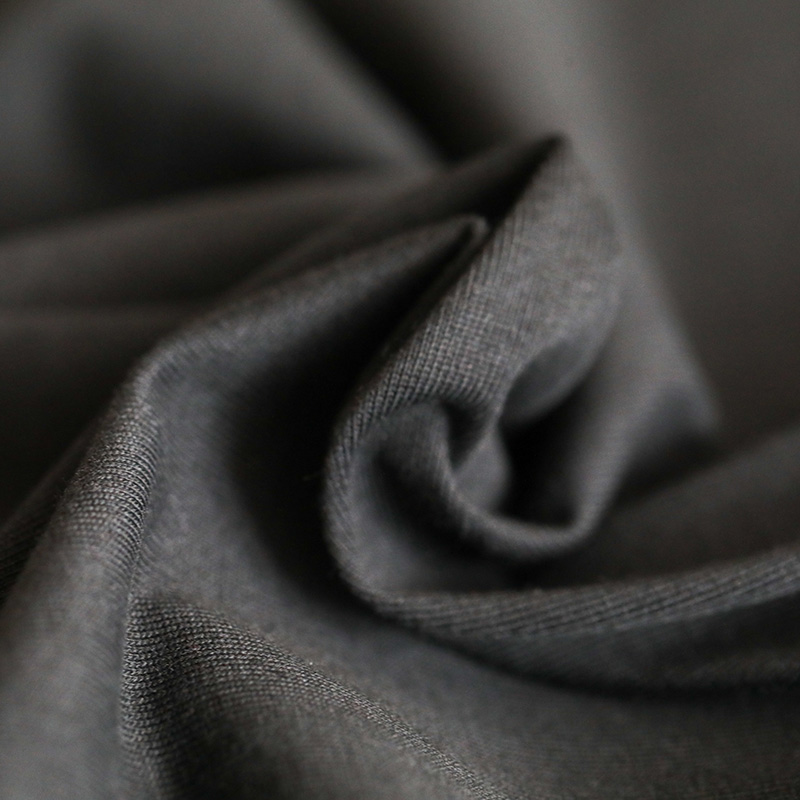
Dehairing/Singeing
Burning off the surface fuzz on fabric can improve the gloss and smoothness, enhance resistance to pilling, and give the fabric a firmer and more structured feel.
The process of burning off the surface fuzz, also known as singeing, involves passing the fabric swiftly through flames or over a heated metallic surface to remove the fuzz. The loose and fluffy surface fuzz quickly ignites due to the proximity to the flame. However, the fabric itself, being denser and further away from the flame, heats up more slowly and moves away before reaching the ignition point. By taking advantage of the different heating rates between the fabric surface and the fuzz, only the fuzz is burned off without damaging the fabric.
Through singeing, the fuzzy fibers on the fabric surface are effectively removed, resulting in a smooth and clean appearance with improved color uniformity and vibrancy. Singeing also reduces fuzz shedding and accumulation, which are detrimental to dyeing and printing processes and can cause staining, printing defects, and clogged pipelines. Additionally, singeing helps to mitigate the tendency of polyester or polyester-cotton blends to pill and form pills.
In summary, singeing improves the visual appearance and performance of the fabric, giving it a glossy, smooth, and structured appearance.
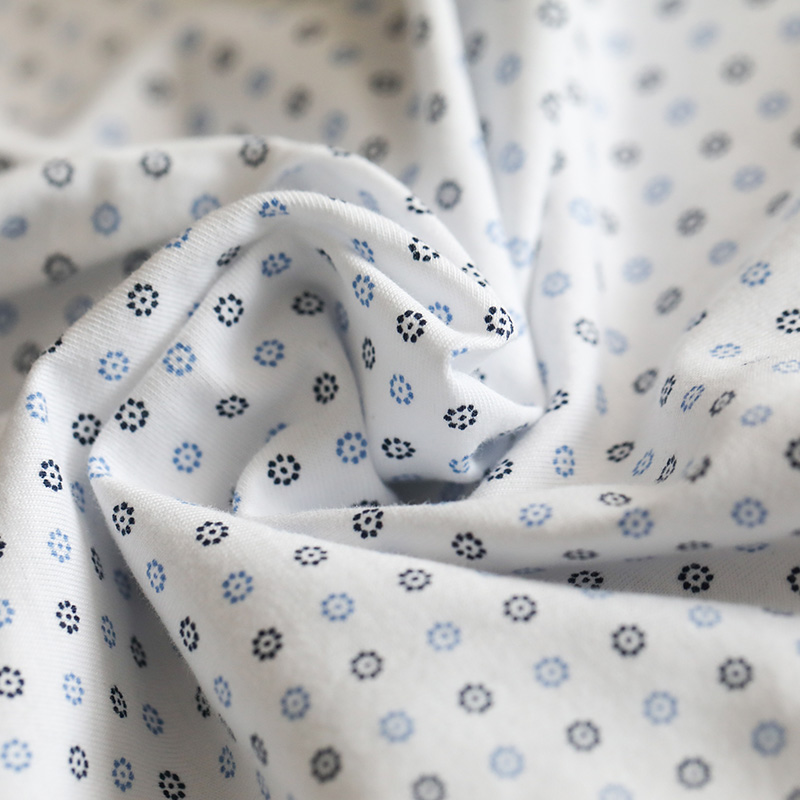
The silicon wash
The silicon wash on fabric is carried out to achieve some of the effects mentioned above. Softeners are generally substances that have the smoothness and hand feel of oils and fats. When they adhere to the fiber surface, they reduce the frictional resistance between the fibers, resulting in a lubricating and softening effect. Some softeners can also crosslink with reactive groups on the fibers to achieve wash resistance.
The softener used in silicon wash is an emulsion or micro-emulsion of polydimethylsiloxane and its derivatives. It imparts a good soft and smooth hand feel to the fabric, replenishing the natural oils lost during refining and bleaching processes of natural fibers, making the hand feel more ideal. Moreover, the softener adheres to natural or synthetic fibers, improves smoothness and strength, improves the hand feel, and enhances the garment performance through certain characteristics of the softener.
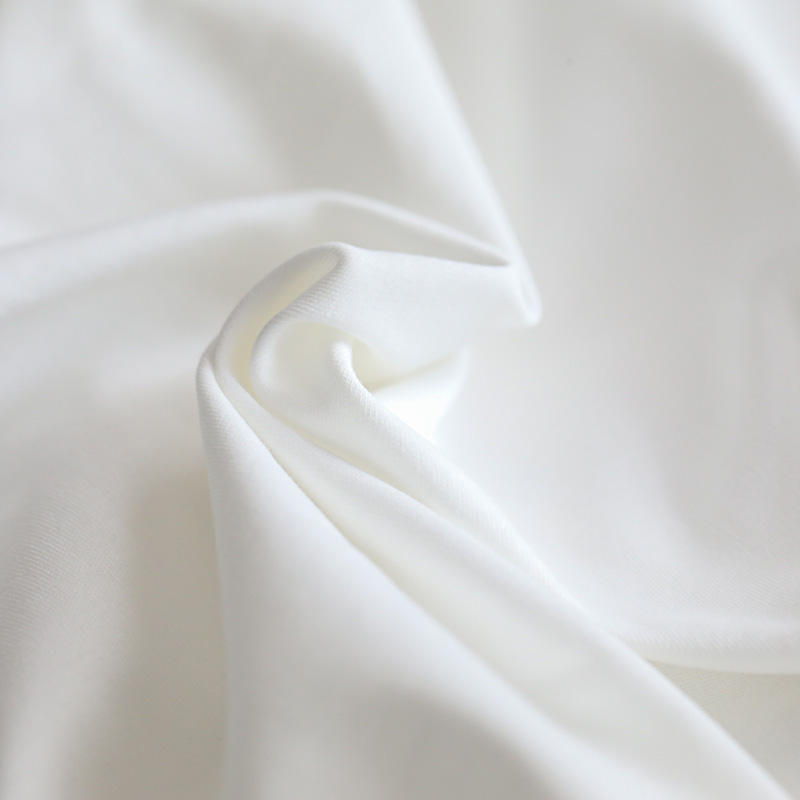
Mercerize
Mercerize is a treatment method for cotton products (including yarn and fabric), which involves soaking them in a concentrated caustic soda solution and washing off the caustic soda while under tension. This process increases the roundness of the fibers, improves surface smoothness and optical properties, and enhances the intensity of reflected light, giving the fabric a silk-like luster.
Cotton fiber products have long been popular due to their good moisture absorption, soft handfeel, and comfortable touch when in contact with the human body. However, untreated cotton fabrics are prone to shrinkage, wrinkling, and poor dyeing effects. Mercerize can improve these shortcomings of cotton products.
Depending on the target of mercerize, it can be divided into yarn mercerize, fabric mercerize, and double mercerize.
Yarn finishing refers to a special type of cotton yarn that undergoes high-concentration caustic soda or liquid ammonia treatment under tension, which improves its fabric properties while retaining the inherent characteristics of cotton.
Fabric finishing involves treating cotton fabrics under tension with high-concentration caustic soda or liquid ammonia, resulting in better gloss, greater resilience, and improved shape retention.
Double mercerize refers to the process of weaving mercerized cotton yarn into fabric and then subjecting the fabric to be mercerized. This causes the cotton fibers to swell irreversibly in concentrated alkali, resulting in a smooth fabric surface with a silk-like luster. Additionally, it improves strength, anti-pilling properties, and dimensional stability to varying degrees.
In summary, mercerize is a treatment method that improves the appearance, handfeel, and performance of cotton products, making them resemble silk in terms of luster.
RECOMMEND PRODUCT